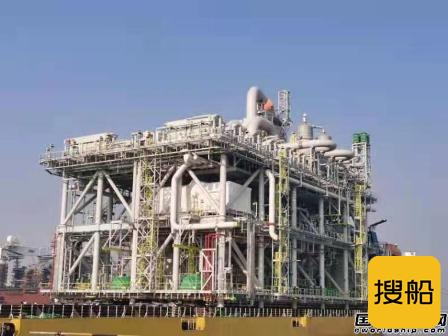
12月28日,青岛武船麦克德莫特海洋工程有限公司MEG模块装船,起运至美国德克萨斯州,标志着由石化四建第一工程公司青岛海洋石油工程项目部参与建造的目前世界上最大的乙二醇装置采用模块化建造的项目,产能110万吨/年,模块总重近40000吨的庞然大物顺利完工起航。
工程项目部负责武船MEG工程3个(PAU01/PAU02/PAU04)模块的115台套设备,共计5616吨安装工作,以及1个模块(PAU05 )管线22680吋D安装和185吨管支架的预制安装工作。
首次承接传统装置模块化。
2020年石化四建公司首次当选天津海洋装备产业(人才)联盟副主席单位。
建设海洋强国已被融入国家“两个一百年”奋斗目标。
石化四建第一工程公司青岛海洋石油工程项目积极推进市场,将海洋模块业务作为加速项目新动能引育和推进高质量发展的重要战略。
和以往模块建造不同,此次承接的武船MEG模块是传统装置模块化施工的典型代表,也是工程项目近年来的又一标志性工程。
大口径焊接之最。
工程项目完成超大直径设备连接管线焊接。
该管线为不锈钢材质,直径两米,壁厚20.6毫米,包括两个三通、两个弯头和两个大小头,每个管件平均质量达到6吨,共5道焊道、492吋,焊接完成总量达到38吨。
在施工前,石化四建第一工程公司工程项目部组织焊接专家与武船乙二醇工程项目业主就超大口径设备连接管道施工方案进行探讨,确定可操作性的施工方案,将初定的现场安装改为车间预制,完成模块化后再进行现场安装,优化后的施工方案不仅将施工周期缩短了三分之一的,还避免了高空作业带来的安全风险。
管道直径达到两米,焊接后容易发生热收缩,变形较大错皮4毫米,焊口成椭圆形。
为了保证焊接质量和进度,施工人员在管线内用千斤顶调整焊口,在管内壁用打磨机打磨内坡口,4道82吋焊口的组对时间仅用5天,一次性报检合格。
为了节省不锈钢管线的充氩时间,施工方案采用充氩塞进行焊道局部充氩,3个小时氩气就可以达到焊接条件,有效达到管线焊道内部充氩的效果。
充氩塞第一次应用于超大口径有色金属焊接,对于超大口径管线可以缩短充氩的时间和有效的在焊接过程中防止不锈钢管线氧化。
在焊接过程中,两名焊工在焊口两侧同时进行打底焊接,焊接作业开始,过程中不能中断焊接作业,经过7个小时的连续焊接,成功完成一道82吋焊道打底。
“有里有面”有技术。
机械专业设备安装包括3台压缩机组,以及4台大型塔器设备,以及653吨内件。
115台设备中有8台设备需要侧装,安装难度大。
项目压缩机组的安装要求结构底座水平度达到0.5毫米,采用现场机加工的方式对底座水平度进行处理。
确保压缩机组安装完成后水平度达到指定要求。
MEG工程四台大型塔器设备总重量达到2206吨,其中最重单台设备达到826吨。
设备吊装集中在2019年12月25日至2020年1月10日。
针对4台塔器的吊装,在设备吊装前工程项目现场人员与业主方反复确认方案,规避现场碰撞问题。
同时对结构底座进行测量水平度,根据结构水平提前设计下料设备调平垫板。
设备吊装前技术人员,测量人员以及现场工人全部就位,设备就位后立即进行测量、调整位置垂直度等工作。
在一切就绪后立即进行焊接,每台塔器设备摘钩前均需要外侧满焊10毫米焊脚高度。
在项目的精心策划下,单台塔器吊装最快24小时内完成摘钩。
前后4台塔器仅耗时11天完成,提前计划4天,获得了业主的一致好评。
工程项目塔内件安装总计653吨,涵盖15种内件形式。
包括规整填料、散装填料、箱式塔盘、烟囱塔盘、除沫器、分布管、降液管、气相分配器等。
内件安装单件最重820公斤,且全部为密闭空间施工作业安装难度极大。
安装前对施工人员进行专项安全培训、技术交底,明确安全风险、安装难度,做好风险防范措施、安装方法。
确保施工安全顺利进行。
由于安装量大,为了在指定工期内完成安装任务,对于材料到货错误、塔体与内件安装碰撞等问题现场与厂家以及业主制定现场修改方案,施工执行两班倒的作业计划。
最终在指定工期内完成了全部内件安装。
由于需要侧装的设备较多,工程项目部制定了利用侧装平台加搬运时坦克车结合的施工方案。
提前预制设备侧装平台,在侧装平台上安装轨道利用搬运式坦克车进行设备侧装工作。
此方案较传统方案完全规避了对大吨位倒链的依赖,侧装主要依靠平台接坦克车进行。
提高了设备侧装工效,大大降低了安全风险。