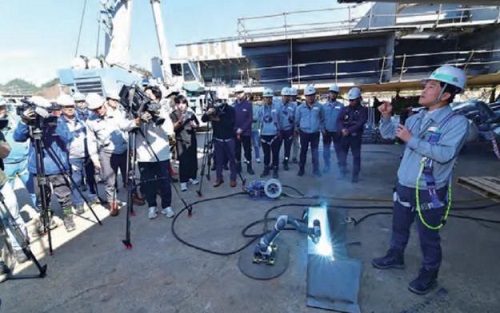
图1 现代三湖重工举行协作机器人及自动焊接设备演示会(图源/现代三湖重工官网)
随着近年来高附加值和环保船舶订单的不断增加,韩国造船业在迎来高景气周期的同时,却因熟练劳动力严重短缺而备受困扰。
为此,韩国三大造船企业正在加快引进协作机器人(Cobot)等自动化、机械化设备,全力构建现代化设备体系,在缓解“用工荒”,提升作业质量、效率和安全性的同时,为转型为数字化智能船厂奠定基础。
HD韩国造船海洋旗下三家造船子公司都在不断加大投资引进各种机器人等自动化设备,特别是现代三湖重工在机器人应用方面跑出了“加速度”,成为韩国船企推进自动化和智能化的“后起之秀”。
韩华海洋(原大宇造船海洋)在重点围绕焊接和涂装作业推进机器人技术应用的同时,计划斥资2亿多美元将目前10%左右的机器人自动化率最高提升至70%,引领未来海洋产业模式转换。
三星重工大力推进船舶建造工序中的自动化、无人化作业转型,并已开发出适用于薄膜型货舱焊接作业的激光高速焊接机器人,有望在此基础上大幅提高LNG运输船的建造效率,降低生产成本。
HD韩国造船海洋3家造船子公司加大投资引进机器人,现代三湖重工跑出“加速度”。
为增加自动化、机械化设备设施,提高生产效率,HD韩国造船海洋2023年在造船、海工领域投资4555亿韩元(约合3.45亿美元),同比增幅达54.7%,其中相当部分用于机器人等设备的引进。
HD韩国造船海洋旗下造船子公司HD现代重工是韩国造船业首家推出协作机器人的船厂。
2018年,HD现代重工首次在大组装工程中引进协作机器人,该型协作机器人通过配备检测异常电流或碰撞的安全功能,能够与人类共同工作。
此后,HD现代重工又对该型协作机器人进行了改进,使其重量減少了一半以上,更加便于运输,并可以在垂直以及水平方向上以人字形模式进行割炬和焊接。
HD现代重工2023年在造船、海工领域投资662亿韩元(约合5000万美元)用于设备设施建设,超过了2022年的620亿韩元。
该公司计划开发相关自动化设备,将此前旨在提高大型船舶强度的船体构件切割由手工作业转变为自动化作业,不仅可以节省一半左右的工时,还能减少切割误差。
2022年10月, 现代三湖重工在机器人应用上也迈出了重要一步,该公司与现代机器人公司(Hyundai Robotics)联合研发的机器人实现了子组件焊接过程的完全自动化。
6个工业机器人同时参与焊接,利用最先进的图像处理技术自动提供焊接线的轨迹。
此外,各个方向的焊接成为可能,通过一种特殊的数字焊接技术,即气体金属弧焊(GMAW),最大限度地减少了焊渣的产生,提高了焊接质量。
2023年8月,现代三湖重工宣布将引进24台新型Universal Robot(UR)协作机器人,但由于生产现场工作量大增,劳动力不足等问题依然存在,因此决定增加引进协作机器人的数量,在年内共引进40台协作机器人,为生产现场提供支援。
10月18日,现代三湖重工举行协作机器人及自动焊接设备演示会(如图1所示),向韩国中小造船研究院等公共机构和外部合作企业介绍了现场应用成果,并表示将为合作企业引进及扩大相关设备提供技术援助。
10月20日,现代三湖重工抽调其自动化创新中心负责自动化焊接的部分人员成立“机器人控制开发组”,作为公司引进焊接协作机器人的开发和管理部门。
公司内部还设有根据需求提供协作机器人手臂、机器人抓手及相关软件等系统整合(SI)的组织。
现代三湖重工表示,其引进的协作机器人使用方便,即使是非熟练技术工人,只要接受最低限度的培训就可以实施自动焊接。
此前,韩国造船业曾使用过自动焊接小车等机械化设备,但1名工人很难同时使用多种设备,且现有的自动焊接小车每天只能进行36次作业,而协作机器人可以超越这种局限。
现代三湖重工引进的彩虹机器人(Rainbow Robotics)和universal Robotics (UR)协作机器人,1名工人可以同时使用2台,只要接受了最基础的培训,任何人都可以进行优质的焊接作业。
这些机器人每天可进行50次作业,实现效率的最大化。
现代三湖重工之所以大幅增加在机械化和自动化领域的投资,加快引进协作机器人,主要是为了解决订单暴增与劳动力短缺的巨大矛盾。
据 统 计,2021年至2023年,现代三湖重工总计承接了超过208亿美元的新船订单,目前的手持订单量在HD韩国造船海洋的3家造船子公司中最为充沛,已经确保了3年以上的稳定作业量。
但由于造船业在韩国被称为“脏累险”的3D(Dirty,Difficult,Dangerous)工种,已成为韩国年轻人回避的职业,船厂正面临严重的劳动力短缺问题。
随着韩国政府改进外籍劳工引进政策,目前现代三湖重工的合作公司(转包企业)中已有超过3000名外籍劳工在生产现场工作,在一定程度上缓解了一线劳动力不足的困难。
不过,随着高附加值船舶订单的增加,船厂对高级技工的需要更加迫切,而这些高素质的劳动力主要还是要依靠韩国国内提供,但目前韩国年轻人却并不愿意到船厂工作。
仅在今年,现代三湖重工还存在500名左右高级技工的需求缺口,因此,能够为生产现场提供援助的协作机器人等自动化设备的重要性正日益提高。
现代三湖重工自动化创新中心常务柳相勋表示 :“为了解决劳动力短缺问题,加快引进协作机器人是必不可少的。
公司正在根据协作机器人的技术开发速度和生产现场对协作机器人的需要推进机器人的使用,估计可以代替所有焊接工作的20%以上。
”
现代三湖重工强调,劳动力短缺将成为造船业的趋势性问题,船企应增加在机械化和自动化领域的投资,进一步提高作业效率。
同时,对于扩大协作机器人应用是否会与为保护工人就业的公司工会产生不和谐的可能性,柳相勋表示 :“与普通机器人不同,协作机器人是和工人一起工作的角色。
工会成员也认识到了劳动力短缺问题的严重性。
因此,加大协作机器人应用对劳资双方来讲都是积极的因素。
通过工会和机器人研发人员之间的合作,公司正在开发更加具有现场亲和力的机器人。
”
HD现代尾浦造船在2022年投资1078亿韩元(约合8100万美元)的基础上,2023年编制了577亿韩元(约合4300万美元)的预算用于造船设备设施建设。
据悉,该公司已推出了制作机舱分段时使用的T-bar carriage、V-ROD carriage、Electric carriage 3种自动化焊接小车。
这些设备在制作1800TEU集装箱船的机舱分段时,示范应用结果显示,自动化率提高了13%。
HD现代尾浦造船计划通过追加投资,将这3种焊接设备扩大应用到其他船型分段的制作,提高生产质量和生产效率。
2023年11月21日, 现代尾浦造船成立“数字生产革新中心”,其任务是通过开发生产自动化指向设计系统、构建以制造革新平台为基础的信息物理系统(Cyber Physical System,简称CPS),实现生产的机械化、电动化、自动化,营造最适合船舶建造现场的数字制造环境。
该中心还将开发贯通设计 -生产数据的数字制造平台,并与HD韩国造船海洋合作,对旗下的HD现代重工、现代尾浦造船、现代三湖重工3家造船子公司的自动化装备要素技术进行验证。
现代尾浦造船计划,到2025年为止,将以内业工程为中心,引进曲面板成型机器人、加工机器人、注塑机器人、龙门式Slit机器人、面板焊接(SAW)机器人等自动化设备,“数字生产革新中心”将利用虚拟模型(在具有与实际相同特性的虚拟空间进行的模拟试验)来验证新技术。
此外,该公司还计划在2023年7月26日到2024年5月期间,对超过1700名生产技术员工进行40次数字化转型体验培训,培训课程包括工业机器人和协作机器人示范等。
据悉,在HD韩国造船海洋的统一规划下,HD现代重工、现代三湖重工、现代尾浦造船正在联合推进基于数字化的“造船未来战略(Future of Shipyard,FOS) ”项目,并计划在2030年之前转型成为智能船厂。
HD韩国造船海洋计划,第一步是到2025年为止,在现代尾浦造船的内业工程中引进各种机器人等自动化设备,并完成与设计联动的CPS的构建,实现内业工程的数字自动化。
此后,将把现代尾浦造船的制造自动化体系与HD现代重工和现代三湖重工正在开发的新一代设计平台合并,将设计到制造的数据作为一个平台进行管理。
通过实施这一计划,HD韩国造船海洋将完成应用于所有造船子公司的基于数字孪(Digital Twin)技术的综合革新平台。
该平台完成后,将对在生产现场收集的数据进行分析,掌握问题所在,并以此为基础实现修改设计的“船舶建造良性循环”过程。
通过这些措施,有望进一步提高船舶的建造质量和施工效率。
韩华海洋超80台机器人应用,投资超2亿美元将机器人自动化率提升至70%。
韩华海洋从2017年开始开发人工悄�(AI)热加工机器人(如图2所示),2020年9月经过内部试用和演示,于10月在其旗下玉浦造船厂的加工车间正式投入使用。
该型机器人被命名为“Goknuri”,也是全球造船业首款将AI技术应用于热加工作业的机器人系统。
“Goknuri”可在改善作业环境的同时,提高产品精密度和生产效率,而且通过与设计数据相连接,也可适用于冷加工作业。
韩华海洋计划通过“Goknuri” 实现作业内容的数据化,并将积累的数据用于其他船舶施工作业。
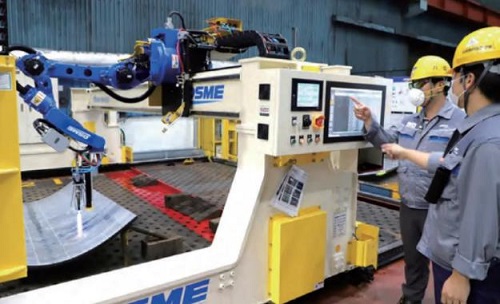
图2 韩华海洋开发的全球造船业首个AI热加工机器人“Goknuri”(图源/韩华海洋官网)
同时, 韩华海洋从2019年开始着手研发焊接协作机器人。
经过数十次的调整改进,在2023年年初,成功开发出可安全地与作业者近距离无障碍协作的碳素钢管焊接机器人(如图3所示),并应用于其玉浦造船厂的作业现场。
该型协作机器人已通过韩国机器人使用者协会(KORUAk)的审查,获得了“协作机器人安装作业现场安全认证”。
这也是韩国首次在没有设置安全围栏和安全传感器的情况下,在现场使用协作机器人。
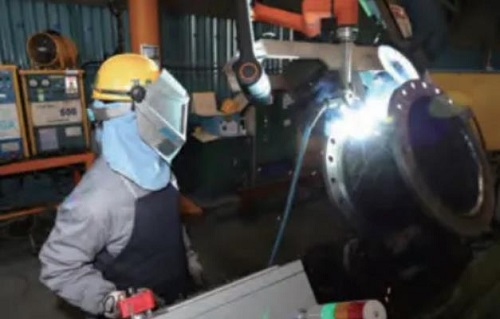
图3 可安全地与作业者近距离无障碍协作的碳素钢管焊接机器人(图源/韩华海洋官网)
此前,在进行碳素钢管焊接作业时,作业者需要亲自移动重量超过30公斤的喷焊工作台,并在手动调整位置后进行焊接,因此如果需要更换焊接位置,准备过程需要花费很多时间,成为提高生产效率的绊脚石。
另外,在引进工业机器人后,为了完成精密焊接并应对焊接过程中的种种变数,作业者需要近距离与机器人进行协同作业,但为了防止作业者与机器人发生碰撞,现有的机器人与作业者之间又必须设置安全围栏,因此无法进行精密焊接。
据了解,该型碳素钢管焊接机器人重量仅为17公斤,使用时无需另行设置安全围栏,只需工作人员按下按键,即可在极其有限的密闭空间内自动进行精密焊接作业,熟练程度相当于具有3年工作经验的焊接技师。
韩华海洋表示,随着该型焊接机器人应用于现场,作业准备时间减少了约60%,不仅提高了生产效率,提升了作业的精确度与质量,还可解决工人短缺问题。
该公司计划持续进行技术开发,将这种目前仅应用于船舶管道的合管(Control pipe for ship)焊接作业的机器人应用于普通管道焊接。
该公司焊接技术研究组组长朴钟民表示 :“女性员工和非熟练技术工人也可以操作这种机器人,有望解决焊接高级技师短缺的问题。
”
据悉,韩华海洋“数字生产中心”2021年4月投产运营后,积极利用各种数据和机器人技术,正在谋求以焊接和涂装为中心的生产现场作业工程的自动化。
目前,韩华海洋在生产现场使用的包括协作机器人在内的机器人已经超过80台,应用于10多个工种。
该公司计划追加投资3000亿韩元(约合2.3亿美元),将目前10%左右的机器人自动化率最高提升至70%,在应对生产熟练工人减少的同时,引领未来海洋产业模式转换。
为此,韩华海洋计划首先确保将物联网、AI等尖端数字技术与船舶生产相结合的自动化工程的安全性,在此基础上通过构建最优生产工艺体系和基于自动化、数字化的船厂,以机器人等自动化设备代替高风险、高难度作业。
韩华海洋在其玉浦造船厂现场构建的自动化生产线还融合了最新的AI、传感器、IOT技术,正在加速实现智能化。
特别是以高危作业领域——钢板预处理及涂装工程为中心,该公司致力于持续进行自动化、无人化设备研发。
针对船舶建造后续工程相关作业,韩华海洋还将在韩国造船业中率先开发无轨焊接系统、电缆敷设自动化设备等,并普及到生产现场,在提高安全性的同时提升生产效率。
韩华海洋希望通过此举, 实现构建所有人都可轻松工作的安全造船厂与基于大数据的智能船厂文化相融合的“绿色&智能船厂(Green&Smart Shipyard)”目标。
与HD韩国造船海洋的3家造船子公司一样,韩华海洋的机器人研发与应用有着先天的优势。
HD韩国造船海洋的母公司HD现代旗下拥有现代机器人公司,其一直在向HD现代重工、现代三湖重工等供货。
2023年10月, 韩华海洋的母公司韩华集团将其旗下韩华Momentum负责制造协作机器人和自动导引车(AGV)的业务分离出来,单独设立了韩华机器人公司,该公司计划与韩华海洋在自动化领域开展技术交流并寻求合作。
三星重工成功研发激光高速焊接机器人,助力LNG运输船建造效率大幅提升。
近年来,三星重工在全球LNG运输船订单潮中承揽了大量订单,进一步稳固了其作为全球最大单体船厂的地位。
克拉克森的数据显示,截止2023年底,三星重工手持订单共计144艘、1046万CGT,按CGT计占全球手持订单总量的8.3%,位居全球首位。
而在三星重工的手持订单中,LNG运输船又位居第一,共计80艘、688万CGT,按CGT计占比高达66%,同样高居全球第一。
为应对前所未有的LNG运输船等环保船舶订单,培育相关建造力量,提高建造效率,三星重工2023年在造船、海工领域投资1515亿韩元(约合1.15亿美元),同比增幅达262.11%,主要用于机器人应用和AI领域的制造革新。
针对船厂熟练焊接技能人才不足,以及等离子电弧焊在提高生产效率方面存在的局限性,韩国造船业要求开发新的焊接技术的呼声一直不断。
为此,三星重工生产技术研究中心从2021年开始进行研发,根据激光焊接技术的应用特性,历经2年开发出了适用于薄膜型货舱焊接作业的高速焊接机器人(如图4所示)。
2023年9月21日,三星重工正式发布了这一成果。
与现有的等离子电弧焊接(PAW)方式相比,该型激光高速焊接机器人的速度最快可提高5倍左右,有望大幅提高LNG运输船的建造生产效率。
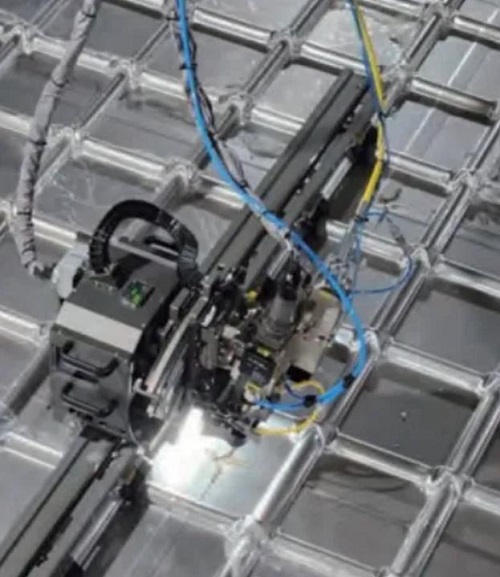
图4 三星重工开发的适用于薄膜型货舱焊接作业的高速焊接机器人
该型激光高速焊接机器人的特点包括 :使激光束以一定间隔和速度旋转的摇摆焊接(Wobble);利用离焦量 (Defocusing)技术,可以生成广阔的堆焊(Weld)宽度 ;内置激光位移传感器,可以自动找到弯曲的焊接位置。
在2米长的薄膜面板焊接时,等离子电弧焊需要5分钟左右,而激光焊接的速度却加快到只需1分钟,因此正在成为大幅提高LNG液货舱工程生产效率的革新技术。
三星重工已在2023年8月成功完成了在韩国LNG型液货舱(KC-2C)上应用激光高速焊接机器人的测试,并在年内完成法国GTT的LNG液货舱(MK-Ⅲ)应用测试后,经过订购方的最终使用许可,正式应用于生产。
三星重工生产技术研究中心主任崔斗真表示 :“激光高速焊接机器人将成为在LNG运输船的核心工程——液货舱制造方面保持压倒性竞争力的核心技术。
今后,公司还计划将其扩大应用到超低温液氢运输船的液货舱。
”
目前,三星重工巨济造船厂的船舶建造工序中的自动化、无人化作业转型也在快速推进中。
据悉,该船厂负责搬运重型材料的叉车已在2022年采用无人化技术,船舶制造所必需的焊接工序也将被多种焊接机器人代替。
巨济造船厂厂长尹钟贤表示 :“我们计划推出小型化、轻量化的焊接机器人,可以在任何工作场所移动工作。
”
同时,近年来大力推进“智能SHI(Smart Samsung Heavy Industries)”数字化转型战略的三星重工正在集中推进物联网、数据自动化技术等的生产体系智能化,以及通过机器人处理自动化(RPA,Robotic Process Automation)等办公自动化技术提高生产效率。
因此,除了在生产现场广泛应用协作机器人外,三星重工还在聊天机器人领域走在了业界前列。
该公司继在2022年开发并应用基于AI技术的对话型设计聊天机器人(ChatBot)之 后,2023年3月又宣布正在加快开发新型聊天机器人“SBOT”(如图5所示),并应用于船舶设计等工作。
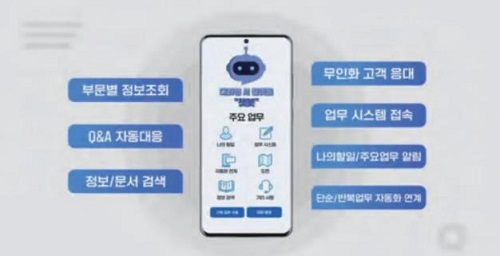
图5 三星重工开发的基于人工智能(AI)的聊天机器人“SBOT”(图源/三星重工官网)
三星重工计划, 今后将对“SBOT”进行升级,使其适用于手机等移动设备,同时添加语音识别等功能,并将应用范围扩大到营销、采购等业务领域。
值得一提的是,三星重工还计划将“SBOT”与美国OpenAI研发的聊天机器人程序“ChatGPT”相连接,提高聊天机器人服务能力。
韩国造船界人士指出,随着订单的不断增长,在劳动力资源不足的情况下,预计三大船企以机械化、自动化为中心的投资今后仍将持续下去。
同时,三大船企都在抓紧向高效率、低成本的智能船厂转型,并计划将相关技术和设备移植推广到合作公司,构筑完备的智能生态体系。
在这一过程中,机器人的广泛应用也将成为大势所趋。
此外,韩国协作机器人界相关人士表示,与工业机器人更倾向于自主运行,执行重复性的、高精度的任务不同,协作机器人是一种与人类共享工作空间,甚至直接与人类进行物理接触的机器人,更多地关注与人类的协同工作和安全协作,以实现更高效的生产。
同时,韩国政府也正在放宽协作机器人使用相关规定,韩国雇佣劳动部决定,根据船厂作业特点制定新的安全规定,代替现有的使用协作机器人时必须设置安全围栏的规定。
从韩国协作机器人市场整体来看,尽管截至目前仍被汽车及电子产业所主导,但由于韩国造船业近年来不仅出现了严重的劳动力短缺问题,而且生产现场安全事故频发,因此船厂引进协作机器人的呼声也越来越高,预计短期内使用机器人的比重将大幅增加,同时随着技术的发展,使用范围还将进一步扩大。